Understanding the Significance of **Injection Mould China** in Modern Manufacturing
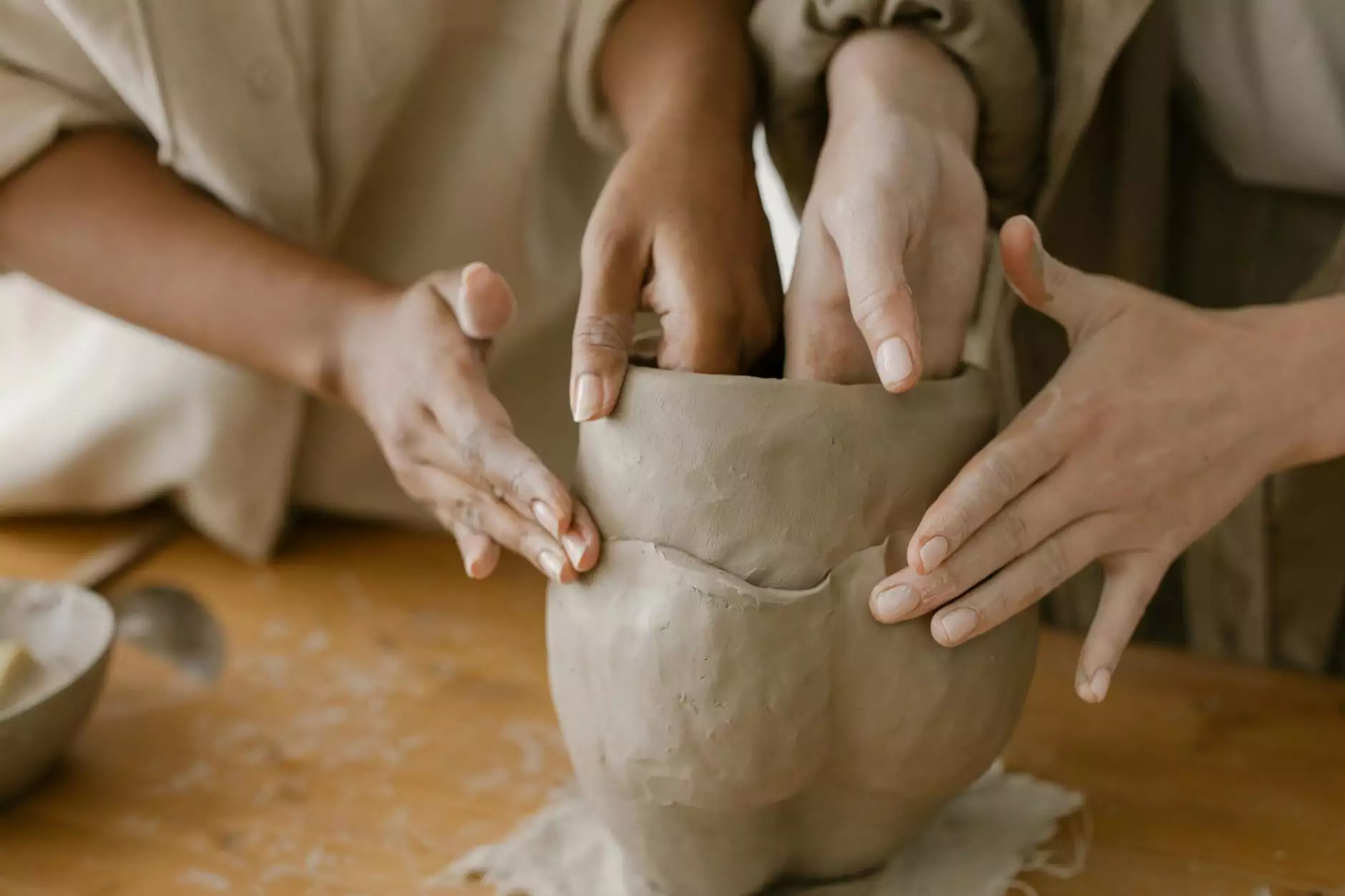
In today's fast-paced manufacturing landscape, businesses are always searching for cost-effective, efficient, and innovative solutions to produce their products. One of the most reliable approaches to achieving these goals is through injection moulding, particularly when it comes to sourcing from China. With a robust industrial framework and a reputation for high-quality production, China has emerged as a key player in this domain.
The Rise of Injection Moulding in China
Injection moulding is a manufacturing process used to produce parts by injecting molten material into a mould. This process has been pivotal for various industries such as automotive, consumer goods, electronics, and more. The reason for the burgeoning popularity of injection moulding in China can be attributed to several factors:
- Cost-Effectiveness: China offers competitive pricing for mould production due to lower labor costs and established supply chains, making it a preferred destination for many businesses.
- Technological Advancements: With continual investments in technology, Chinese manufacturers have adopted modern techniques that enhance production efficiency and precision.
- Scalability: Chinese manufacturers like Hanking Mould can easily scale operations to meet the demands of small and large-scale production runs.
- Expertise: Years of experience in the field have led to a wealth of knowledge, resulting in high-quality moulds that lead the industry.
Choosing a Reliable Injection Mould China Manufacturer
When it comes to selecting a competitive partner for injection moulding, the following considerations should guide your decision:
1. Experience and Reputation
Look for a manufacturer like Hanking Mould that has a proven track record in the industry. Experience often speaks volumes about the reliability of a manufacturer.
2. Quality Assurance
Quality control measures are paramount. Ensure that the manufacturer conducts rigorous testing and adheres to international quality standards to guarantee that the moulds produced will meet your specifications.
3. Customization Capabilities
Your projects may require specific designs—therefore, a manufacturer should be capable of producing customized solutions tailored to your needs. Hanking Mould specializes in creating unique moulds based on the precise requirements of their clients.
4. Communication and Support
Strong communication is essential throughout the production process. Choose a manufacturer that values transparency and offers ongoing support to address any issues that may arise.
The Benefits of Working with Hanking Mould
Hanking Mould, a leading plastic injection mould manufacturer, stands out for several reasons:
High-Quality Materials
The moulds are made using premium-grade materials that ensure durability and longevity, significantly reducing the chances of defects and the necessity for replacements.
Advanced Manufacturing Techniques
Utilizing state-of-the-art technology, Hanking Mould can produce intricate and complex mould designs that cater to diverse industry needs.
Comprehensive Services
The company offers a complete suite of services from design and prototyping to production and after-sales support, making the entire process seamless for clients.
Timely Deliveries
Time is of the essence in manufacturing. Hanking Mould prioritizes on-time delivery, ensuring that clients receive their products as scheduled.
The Process of Injection Moulding
Understanding the injection moulding process can help businesses appreciate the value and efforts involved in producing high-quality parts. Here is a breakdown of the steps involved:
1. Designing the Product
The first step involves crafting a detailed design of the component, ensuring that all dimensions and functionalities are accurately represented. Collaboration between designers and engineers is critical at this stage.
2. Creating the Mould
Once the design is finalized, the next step is to construct the mould itself. This is where precision engineering plays a crucial role, as any inaccuracies can lead to complications during production.
3. Melting and Injecting the Material
After the mould is ready, the chosen plastic material is melted and injected into the mould at high pressures. This step necessitates careful temperature control to achieve the desired properties in the finished product.
4. Cooling and Solidification
Once injected, the material must cool and solidify into the desired shape. Cooling times can vary based on the material and part thickness.
5. Ejection and Finishing
After cooling, the mould is opened, and the finished part is ejected. Any necessary post-processing steps, such as trimming or polishing, are performed to ensure a high-quality finish.
Key Industries Benefiting from Injection Moulding in China
The versatility of injection moulding allows it to serve a wide array of industries. Here are some key sectors leveraging this technology:
- Automotive: From dashboards to bumpers, automotive parts are often produced via injection moulding due to the need for precision.
- Electronics: Many electronic components, such as casings and connectors, are made using injection moulding to offer durability and aesthetic appeal.
- Consumer Goods: Household products, toys, and packaging often rely on injection moulding for cost-effective production.
- Medical Devices: Injection moulding is crucial for the production of high-quality, sterile medical components that meet stringent regulations.
Environmental Considerations in Injection Moulding
As the world shifts toward sustainability, the plastic injection mould industry is also adapting. Manufacturers are now focusing on sustainable practices, which include:
Material Selection
Choosing biodegradable or recyclable materials can significantly reduce the environmental impact of plastic products. Many companies are now opting for eco-friendly alternatives in their injection moulding processes.
Energy Efficiency
Modern injection moulding machines incorporate energy-efficient designs that minimize power consumption during production, contributing to lower carbon footprints.
Waste Reduction
Advanced technologies allow for better material utilization, reducing waste generated during the moulding process. Additionally, companies are increasingly recycling scrap plastic back into production.
Future Trends in Plastic Injection Moulding
The landscape of injection moulding is ever-evolving. Here are some anticipated trends that businesses should be aware of:
1. Automation and Industry 4.0
With the onset of Industry 4.0, manufacturers are integrating smart technologies and automation into their processes, enhancing efficiency and reducing labor costs.
2. 3D Printing Integration
The combination of traditional manufacturing methods with 3D printing is gaining traction. This allows for rapid prototyping and more complex mould designs that were once difficult or impossible to achieve.
3. Smart Materials
Advancements in material science are leading to the development of smart materials that can alter their properties under different conditions, enhancing the application possibilities of injection moulded components.
Final Thoughts on Injection Mould China
When considering injection mould China, it is essential to partner with a reputable firm like Hanking Mould that can provide high-quality solutions tailored to your unique needs. With a blend of experience, advanced technologies, and a commitment to excellence, Hanking Mould is poised to be your go-to source for all your plastic moulding needs. The benefits of embracing injection moulding in China are numerous, ranging from cost efficiency to innovative production techniques. Businesses that leverage these advantages will position themselves ahead of the competition in an ever-evolving marketplace.